Silicone Molds: A Comprehensive Guide to Their Uses
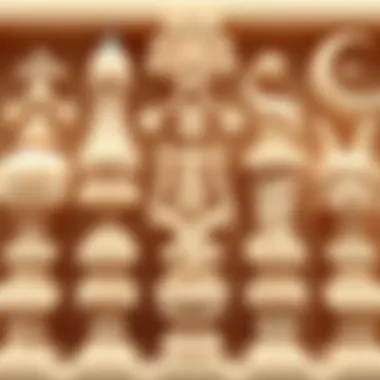

Intro
In today's world, silicone molds have found their way into numerous industries, from baking to manufacturing. These molds provide a flexibility and durability that traditional mold materials often lack. With their increasing popularity, understanding the ins and outs of silicone molds is essential for anyone looking to enhance their creative projects or optimize production processes.
This guide aims to shed light on silicone molds, delving deep into their properties, production methods, and wide-ranging applications. Whether one is a hobbyist whipping up treats in the kitchen or a professional in the manufacturing realm, this article serves as a comprehensive resource to navigate the versatile landscape of silicone molding.
Silicone molds allow for a diverse array of creations, including intricate designs in baking, unique craft pieces, and even components in industrial applications. With their heat-resistance and non-stick characteristics, silicone molds present distinct advantages over conventional materials. By the end of this guide, readers will gain valuable insights not only into the practical uses of silicone molds but also into how to successfully design, utilize, and maintain them to maximize their potential.
Intro to Silicone Molds
Understanding silicone molds is crucial for anyone engaging in diverse creative endeavors, be it in the kitchen baking delightful treats, crafting unique objects, or innovating in industrial applications. Not only do silicone molds offer exceptional flexibility and durability, but they also enhance production efficiency and creativity. This section will lay the groundwork for exploring silicone molds, covering the basic definition of silicone as a material and its historical context in mold usage.
Defining Silicone as a Material
Silicone is a synthetic polymer made up of silicon, oxygen, carbon, and hydrogen. This combination grants silicone its unique properties, setting it apart from traditional materials like rubber or plastic. The material possesses a range of beneficial attributes: it is non-toxic, resistant to extreme temperatures, and doesn't easily retain odors or colors.
One of the remarkable characteristics is its flexibility, allowing it to stretch and reshape without losing structural integrity. In short, silicone molds can withstand high heat in the oven while keeping their form, making them ideal for baking and cooking. They are also entirely safe for food contact, which is a major appeal for home cooks and professional chefs alike.
Moreover, when it comes to intricate designs, silicone’s ability to capture fine details can’t be underestimated. This unique property allows artists and hobbyists to create stunning shapes and structures, from fondant decorations to artistic sculptures.
Historical Overview of Mold Usage
Molds have been used for centuries, tracing back to ancient civilizations. The earliest molds were made from clay and stone, utilized for pottery and casting metals. These methods laid the foundation for what would evolve into the more sophisticated molding techniques we see today.
As technology progressed, mold making transitioned from traditional methods to more advanced synthetic materials. The introduction of silicone in the mid-20th century revolutionized the molding industry; it allowed for a greater variety of applications due to its durability, heat resistance, and flexibility.
Today, silicone molds are pervasive across numerous industries. From the culinary world to high-tech manufacturing, the versatility of silicone has positioned it as a staple material for mold-making. With the rise of custom silicone molds, the accessibility to create personalized products has never been easier, fostering creativity in both professional and hobbyist environments.
"The adaptability and range of applications for silicone molds is astonishing, allowing for unprecedented creativity in various fields."
In the following sections, we will delve deeper into the properties that make silicone ideal for molding and explore its practical applications in everyday life. Understanding the foundation of silicone molds is essential to fully appreciate their significance in multiple domains.
Properties of Silicone That Make It Ideal for Molding
Silicone molds have carved out a solid niche in various industries, from culinary to industrial applications. Their unique properties make them particularly well-suited for a range of molding tasks. This section dives into the critical elements that underscore the advantages of silicone over traditional materials. Each property contributes to why silicone is revered as the go-to choice for both professionals and hobbyists alike.
Flexibility and Durability
One of the hallmark traits of silicone is its remarkable flexibility. Unlike plastics or metals, silicone retains its mold shape without cracking or degrading over time. This is essential in making intricate designs where precision is *vital*. To put it simply, if you want to create a cake that resembles a majestic swan or a flower that seems to bloom right out of the oven, silicone molds are your best bet. The material bends and stretches, making it easy to demold even the most delicate shapes without risking breakage.
Moreover, durability is another defining characteristic. Silicone molds are built to last, often withstanding temperatures ranging from as low as -40 degrees Fahrenheit to up to 500 degrees Fahrenheit. This heat tolerance not only allows for a variety of usages but also seamless transitions between frozen and baked preparations. You can whip up a batch of ice cubes for your drink one moment and bake a soufflé the next, all in the same mold. That's the kind of versatility that keeps folks coming back for more.
Chemical Resistance and Heat Tolerance
Now, let's talk about chemical resistance. Silicone is inherently resistant to a variety of chemicals, which means that solvents, oils, and greases will not harm the integrity of the mold. This trait is particularly advantageous when it comes to industrial applications, where molds may come into contact with harsher substances. Some people even find that silicone can stand up to wear and tear better than traditional materials.
In the kitchen, this chemical resistance offers peace of mind. You can use strong flavoring agents or high-acid ingredients without worrying about damaging your mold. Furthermore, the heat tolerance plays nicely into this equation. Silicone molds can be placed directly into ovens or microwaves, allowing for batter or dough to be cooked without the fear of melting or deforming. Thus, their multifunctional nature is hard to beat when it comes to ensuring a successful outcome in both cooking and crafting endeavors.
Ease of Release and Non-Stick Characteristics
Perhaps one of the most applauded features of silicone molds is their ease of release. When it comes to baking and crafting, the last thing you need is to spend more time chiseling your creation out of a mold than enjoying it. Thanks to the non-stick characteristics of silicone, demolding is a breeze. Whether you're pulling out a batch of pastries or sculptures, you’ll find they pop out with minimal fuss, often requiring no additional oils or sprays.
"If you want your creative pursuits to flow smoothly, silicone molds are your ticket to effortless releases. Say goodbye to tedious scraping and hello to beautifully formed results!"
In summary, these advantageous properties enhance the usability of silicone molds, making them not only user-friendly but a dependable tool for anyone looking to dabble in baking or crafting. Understanding these features informs better choices in material selection and application, ultimately leading to greater success and satisfaction in your projects.
Manufacturing Process of Silicone Molds
The manufacturing process of silicone molds is central to understanding how these versatile tools are made and their subsequent applications. The intricacies involved in producing these molds are what enable them to perform effectively across a variety of domains, from culinary arts to industrial materials handling. Grasping the nuances of this process not only sheds light on their functionality but also holds importance for anyone looking to use or create silicone molds. In this section, we'll explore the different types of silicone employed in molding and walk through the step-by-step production that shapes these practical implements.
Types of Silicone Used in Molding
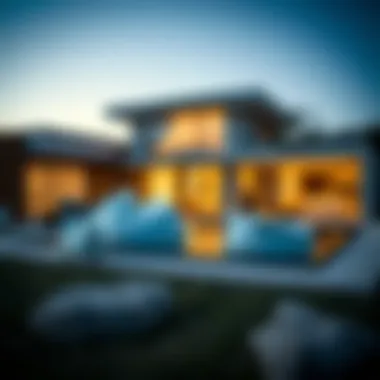
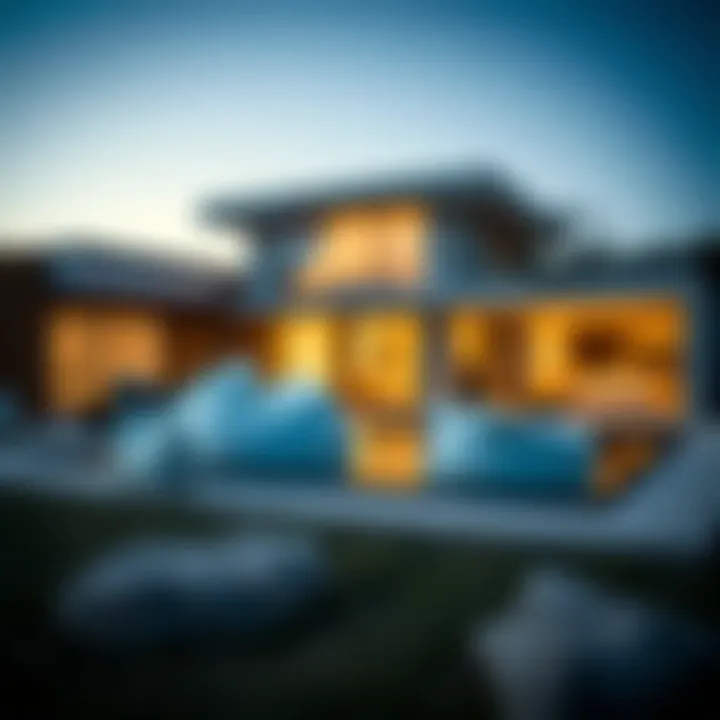
Silicone comes in various forms, with each type possessing distinct qualities that suit specific molding needs. Some common types include:
- Room Temperature Vulcanizing (RTV) Silicone: This type is known for its ease of use. It cures at room temperature and is ideal for hobbyists and small projects where precision isn't extremely critical.
- High-Temperature Silicone: Often utilized in professional settings, this silicone can withstand significant temperatures without losing its structural integrity, making it essential for applications involving heat.
- Liquid Silicone Rubber (LSR): LSR is used in mass production and can handle fine details and complex shapes. Its adaptability lends it well to both high-end crafting and industrial uses.
Each of these types has its own set of advantages, depending on the desired application. The choice of silicone type often depends on the specific requirements of the project and the environment where the mold will be employed.
Step-by-Step Mold Production
Producing silicone molds is not a simple task. Each phase requires attention to detail and an understanding of the materials involved. Let's break down the steps:
Preparation of Materials
Preparation is where the magic begins. Before anything else, the right tools and materials must be gathered, including the silicone, mixing containers, and any additional elements like colorants or reinforcing agents. This initial stage sets the cornerstone for the entire molding process. When choosing materials, it is crucial to ensure they are compatible and of suitable quality to achieve a successful end product. One unique feature of preparing materials is the precision required; even a minor error can lead to mold failure.
Creating the Mold Frame
The mold frame acts as a structural support for what will become a silicone mold. Traditionally, this involves using a sturdy material like wood or plastic that can handle the weight and pressure of the silicone during the curing phase. It is vital that the frame be designed with care, ensuring proper alignment, as any discrepancies could distort the final product. The mold frame’s durability and form are beneficial for construction and longevity, offering stability throughout the pouring process.
Pouring the Silicone
Pouring silicone must be done with careful attention and technique. First, the silicone is mixed according to specified ratios, which is crucial for the mold's attributes. When pouring, avoiding air bubbles is key as these can impact the mold's quality negatively. This step highlights the importance of technique: a steady hand and a slow, controlled pour help in achieving an even distribution that fills all the intricacies of the mold frame.
Curing Process
The curing process is where the silicone transforms from a liquid to a solid state. Depending on the type of silicone used, this process can take anywhere from a few hours to several days. This phase is vital; it solidifies the structure and ensures that all details within the mold are preserved. A unique aspect of curing is the environmental conditions affecting it such as temperature and humidity which must be considered to ensure successful outcomes. Proper curing results in a durable and flexible mold that performs exceptionally well in its intended application.
"The crafting of silicone molds requires precision and a keen understanding of materials; a little extra care can yield transformative results."
Understanding the manufacturing process of silicone molds reveals the commitment to quality and attention to detail that makes them an essential tool in various fields. From baking to industrial uses, the phases of creating these molds dictate their effectiveness, revealing the depth of knowledge necessary to create practical and innovative solutions.
Applications of Silicone Molds
Silicone molds serve a wide array of purposes across various industries, making them an essential tool for both amateur and professional users. From culinary delight to artistic expression and large-scale manufacturing, the applications of silicone molds are extensive and show the material's adaptability. Utilizing silicone molds goes beyond just convenience; it offers significant benefits that can enhance efficiency and creativity in any project.
Baking and Culinary Uses
In the culinary world, silicone molds are becoming a go-to for many bakers and chefs. Their flexibility allows for intricate designs that pop out easily without damaging the finished product. Whether it’s a delicate mousse or a sturdy cake, silicone molds withstand temperature fluctuations, ensuring consistent results.
Some specific culinary applications include the following:
- Fondant Molds: Create beautiful decorations for cakes, allowing for fine details that traditional molds can't offer.
- Chocolate Molds: Perfect for casting chocolates into unique shapes and allowing for even cooling cycles.
- Baking Pans: Versatile in baking, one can easily experience even heat distribution, which is crucial for perfectly baked goods.
Moreover, silicone's non-stick properties reduce the need for greasing, cutting down on additional calories and saving time in cleaning. In a fast-paced kitchen environment, this efficiency can be invaluable.
Crafting and Artistic Applications
The realm of crafting and artistry opens a treasure trove of possibilities with silicone molds. Artists and hobbyists turn to silicone to create custom pieces, as the variety in design is limited only by imagination.
Applications here are multifaceted:
- Resin Art: Using silicone molds to cast resins enables fine detail and intricate designs for jewelry or decorative objects.
- Soap Making: Homemade soaps shaped in silicone molds often reflect personal styles and themes, appealing to both creators and consumers.
- Candle Making: Artists can pour wax into silicone molds to craft unique candle shapes, with easy release ensuring that every piece looks pristine.
Silicone molds in crafting not only enhance creativity but offer a more sustainable option since they are reusable and durable, lowering the need for constant replacements.
Industrial and Commercial Uses
On a commercial scale, silicone molds play a critical role in mass production. Industries such as automotive, aerospace, and consumer goods adopt silicone molds for various applications, ensuring quality and efficiency.
Considering industrial applications, one can identify:
- Parts Manufacturing: Silicone molds can produce components that demand precision, such as seals or gaskets, vital in maintaining product integrity.
- Prototyping: Quick turnaround times in creating prototypes facilitate faster product development, boosting time to market for companies.
- Mass Production: Cost-effectiveness and repeatability during the manufacturing process allows businesses to leverage silicone molds for high-volume outputs.
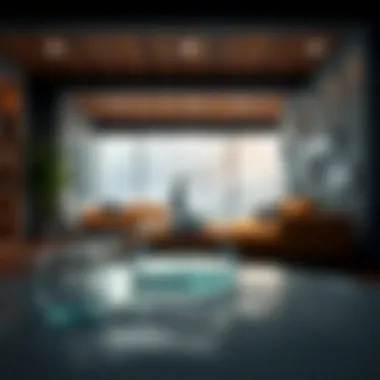
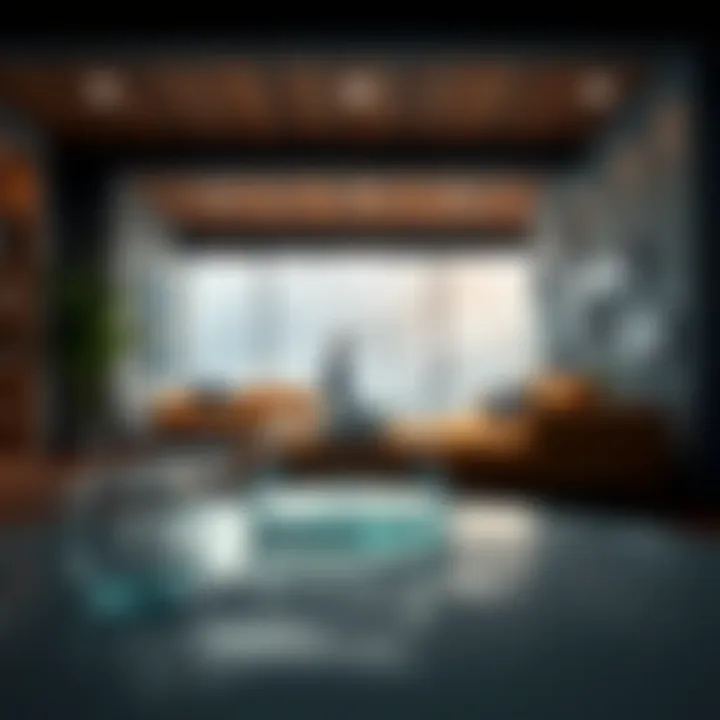
Additionally, their resistance to chemicals and heat makes them invaluable when dealing with tough materials in an industrial setting. The versatility ensures manufacturers don't need to compromise on quality despite quantity.
Advantages of Silicone Molds Over Traditional Materials
The exploration of silicone molds is revealing not just their functionalities but also the advantages that set them apart from traditional materials like metal or plastic. This section focuses on why these silicone molds are not only a boon for creative expression, but also a smart investment for industries ranging from baking to manufacturing.
Cost-Effectiveness
One of the most significant benefits of using silicone molds lies in their cost-effectiveness. Unlike traditional mold materials that often come with a hefty price tag, silicone molds are quite affordable. They have a longer lifespan, meaning less frequent replacements and repairs. This can result in substantial savings over time, especially for businesses that rely on molds for production.
The initial cost might be higher compared to, let’s say, a basic plastic mold, but the durability and performance of silicone often justify the expenditure. For instance, silicone can withstand higher temperatures without warping, which is a common issue with cheaper, traditional molds. This means fewer batch failures and less waste—which can save dollars and cents in an industry's bottom line. “You pay for what you get” rings true here; investing in quality molds can enhance yields in production and cutting back on inefficient processes is a bonus.
- Longer Lifespan: Silicone molds can last years if maintained well.
- Increased Productivity: The resilience of silicone means less downtime due to mold failure.
- Reduced Waste: Say goodbye to frequent replacements due to wear and tear.
Versatility in Design and Usage
When it comes to versatility, silicone molds really hit the nail on the head. They can be used for a wide range of applications, which is something traditional materials often struggle with. For instance, silicone molds are equally effective for baking breads as they are for making intricate soap designs or even for industrial uses like producing parts for consumer products.
This adaptability also extends to their design capabilities. Silicone can be molded into complex shapes and intricate details that other materials might find challenging or impossible to achieve. Want a mold shaped like a giant flower or perhaps a specific animation character? Silicone can do that with ease.
Moreover, silicone molds can easily accommodate a variety of mediums—from food to crafting materials. No matter whether you want to create a cake, a resin art piece, or more practical components, silicone is a jack-of-all-trades in mold-making. It can also handle hot and cold mediums, making it suitable for a multitude of jobs. This level of versatility ensures that users can tackle different projects without feeling hemmed in by their materials.
- Comprehensive Application Range: Baking, crafting, or manufacturing, silicone molds can do it all.
- Intricate Design Capabilities: Creating detailed and complex shapes is a breeze.
- Compatibility with Various Mediums: Suitable for food, resin, plaster, and more.
Ultimately, the advantages of silicone molds serve to bolster efficiency, minimize costs, and expand creative horizons. They provide an edge, especially when used in settings where multiple projects demand reliable and adaptable mold solutions.
Best Practices for Using Silicone Molds
When it comes to silicone molds, understanding the nuances of their use is paramount. Best practices not only protect your investment but also optimize the outcomes of your projects. These molds are widely celebrated for their flexibility and durability, yet improper handling may lead to unwanted results. Here, we outline key practices that can enhance your experience with silicone molds and maximize their effectiveness.
Cleaning and Maintenance
Maintaining silicone molds is fundamental for achieving durable and effective results. Here are several essential tips to ensure your molds remain in top shape:
- Wash After Each Use: It’s vital to clean your molds right after use. Residues from food or craft materials can sit and harden, affecting future batches. Use warm, soapy water with a soft sponge for a thorough yet gentle clean. Avoid harsh chemicals and abrasive scrubbers that could damage the mold surface.
- Dry Completely: Water can cause molds to warp or become discolored over time. Wipe them dry or let them air dry completely before storing.
- Avoid Extreme Temperatures: Silicone can handle quite a stretch with heat, but it’s best to keep it away from very high or low-temperature extremes during cleaning. Using steaming water is not advisable for cleaning since it may affect the mold's integrity.
- Inspect Regularly: Give your molds the once-over every now and then. Check for signs of tears, discoloration, or distortion. Any defects may compromise the final product’s quality.
Regular maintenance ensures that your molds remain effective and lasts much longer than they otherwise might.
In addition to these practices, consider storing your molds properly for added longevity.
Storage Tips
The way you store your silicone molds is just as crucial as how you clean them. Proper storage can prevent warping and prolong the life of your molds:
- Store Flat: Whenever possible, store molds flat rather than stacking them, which may lead to unnecessary creases. If just impossible, placing a piece of cardboard or an old cutting board in-between can help avoid this loss of shape.
- Avoid Direct Sunlight: Long exposure to sunlight can wear down the silicone material. Whether on a shelf or in a drawer, ensure molds are kept out of direct light to maintain structural integrity and color.
- Keep Dust-Free: Dust particles can create some unwanted texture on the surface, leading to issues when pouring. Use cloth covers to keep them dust-free while in storage.
- Temperature Control: Store in moderate temperatures. Too much heat can cause the silicone to change shape or degrade, while extreme cold may make it brittle.
Designing Custom Silicone Molds
When it comes to silicone molds, customization holds a key position. Designing custom silicone molds presents a plethora of possibilities, catering to specific needs whether in baking, crafting, or industrial applications. This tailored approach allows users to create shapes and features that are unique, enhancing both aesthetic appeal and utility. The benefits are far-reaching—custom molds can optimize production efficiency, minimize waste materials, and allow for creativity to flourish.
Factors to Consider in Customization
Designing a custom silicone mold is not a one-size-fits-all process. To ensure the final product meets expectations, several factors should be taken into account:
- Purpose and Application: Clearly define what the mold will be used for. Is it for intricate cake designs, unique craft pieces, or industrial parts? Knowing this helps narrow down design choices.
- Size and Dimensions: Measure twice to cut once. Dimensions are critical. Molds need to fit the intended application snugly to ensure proper functionality.
- Material Selection: Not all silicones are created equal. Some may be better suited for high-heat applications while others offer greater flexibility. Choosing the right silicone can impact durability and ease of use.
- Design Complexity: Think about how intricate your design is. More complexity can lead to challenges in both the creation of the mold and the ease of releasing the final product.
- Budget Constraints: Customization can vary significantly in cost depending on complexity and material. It’s vital to stay within budget while still achieving desired results.
Each of these factors plays an integral role in the development of effective silicone molds, allowing users to create exactly what they envision.
Digital Tools for Mold Design
In an era dominated by technology, digital tools have revolutionized the way custom silicone molds are designed. These tools offer precise control over the design process and can simplify the journey from concept to creation:
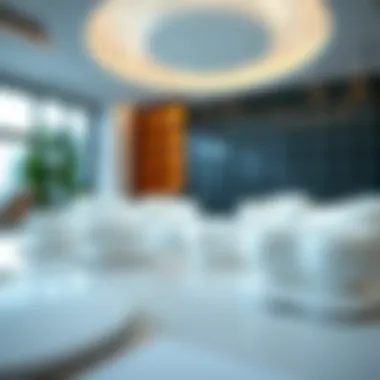
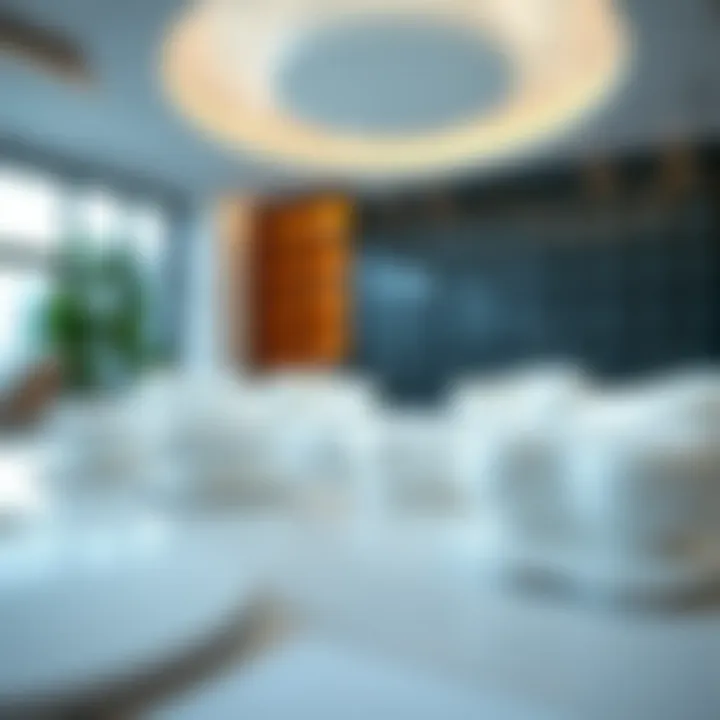
- CAD Software: Computer-Aided Design (CAD) software such as SolidWorks or AutoCAD gives users the ability to create detailed 3D models. It allows designers to visualize the mold before physical production begins.
- 3D Modeling Tools: Programs like Blender or Tinkercad enable users to sculpt highly customized shapes. These are especially beneficial for artistic molds where detail matters.
- Simulation Software: Tools that simulate how silicone behaves during pouring and curing can predict potential issues. This preemptive troubleshooting minimizes waste and time.
- Online Resources: Platforms on the internet such as YouTube or design forums can be valuable for tips and tricks shared by fellow mold designers.
Digital tools enhance the design process, minimizing guesswork and allowing for greater innovation in mold customization. As you embark on designing your custom silicone mold, leveraging these technologies can add a layer of sophistication and reliability to your creations.
In the hands of skilled creators, custom silicone molds become not just tools, but gateways to endless creativity.
By focusing on these essential aspects, individuals and businesses alike can harness the full potential of silicone molds. A well-designed mold is not only a functional item but a key to unlocking new avenues in creativity and production.
Challenges and Limitations in Silicone Molding
While silicone molds are prized for their versatility and ease of use, they come with their own set of challenges and limitations that both professionals and hobbyists must consider. Acknowledging these issues is crucial for anyone looking to successfully utilize silicone molds in their projects. Without understanding what can go wrong or what limitations exist, users may find themselves faced with unexpected hurdles that can derail even the best-laid plans.
Common Issues Encountered
During the process of working with silicone molds, a variety of common issues may arise. Here are the significant headaches that can crop up:
- Bubbles in the Mold: One of the most frequent problems is the formation of air bubbles trapped within the silicone. This usually happens during mixing or pouring, and it leads to imperfect molds.
- Inconsistent Curing: Sometimes, the curing process doesn’t go as planned. Factors such as temperature, humidity, or inadequate mixing ratios can lead to molds that are either too soft or excessively rigid.
- Sticking Issues: Although silicone molds are generally non-stick, certain materials can adhere to the surface. This can be a real kicker when you’re trying to remove your final product cleanly.
- Durability Concerns: If not handled properly, silicone molds can tear or degrade over time. This damage may be exacerbated by exposure to temperature extremes or chemical reactions from the materials used in the mold-making process.
"Understanding these common issues not only helps in preparing for them but also enhances the overall experience of working with silicone molds."
How to Troubleshoot Problems
Addressing challenges requires a methodical approach. Here are several troubleshooting tips to handle common issues encountered with silicone molds:
- Bubbles in the Mold: If you’re dealing with air bubbles, try gently tapping the sides of the mold after pouring the silicone or using a vacuum chamber to remove air. These methods encourage bubbles to rise to the surface and burst.
- Inconsistent Curing: Always follow the manufacturer’s instructions for mixing and curing. If you suspect the temperature is off, consider moving to a more climate-controlled environment until the mold has set properly.
- Sticking Issues: To mitigate sticking, consider using a release agent tailored for the specific material being poured into the mold. Another tip is to season the mold with cooking oil or a silicone-based conditioner prior to use.
- Durability Assurance: To prevent tearing, be gentle when handling your molds. Store them flat and avoid stacking to reduce stress on the material. Always clean them using soft, non-abrasive tools to maintain integrity.
By familiarizing oneself with these challenges and their solutions, users can achieve better results and fully leverage the unique properties of silicone molds. Understanding that mistakes can happen allows for a smoother workflow and enhances the learning process in working with this adaptable material. For further information on silicone molding techniques, resources such as Wikipedia or Britannica provide great insights.
Future Trends in Silicone Mold Technology
Silicone molds have transformed artisanal production and industrial manufacturing alike. Their adaptability and durability are only expected to grow with advancements in material science and production methods. In this section, we explore future trends that can enhance the efficacy and application of silicone molds, offering insights valuable for investors and manufacturers keen on innovation.
Innovations in Material Science
The field of material science is continuously evolving, producing new composite materials that enhance the properties of silicone itself. For example, researchers are working on blends that incorporate nanoparticles to yield molds that are not only more heat-resilient but also harder and more tear-resistant. Such innovations mean that silicone molds can withstand harsher production environments while maintaining the flexibility that makes them so appealing.
Moreover, developments in biodegradable silicone derivatives are something to keep an eye on. With environmental concerns pressing down on many industries, these greener alternatives allow manufacturers to produce molds that perform as well as traditional silicone but with less impact on the planet.
Think about this: a baker could switch to a fully compostable silicone mold while still producing high-quality pastries. This innovation doesn’t just improve sustainability; it aligns with consumer preferences towards responsible sourcing and eco-friendly materials.
"As silicone molding evolves, so does our responsibility to the environment. Innovations in material science not only create better molds but propell the whole industry forward."
The Role of 3D Printing in Mold Production
3D printing has made waves across various fields, and mold-making is no exception. It allows for rapid prototyping, which means designs can be tested and tweaked in real-time. A craftsman with an original design can print a mold in hours instead of weeks. This immediacy fosters innovation, making it feasible for hobbyists to explore intricate designs that were once only available to industrial producers.
Furthermore, custom molds can be printed with silicone-infused filaments specific to the design requirements. This capability not only shortens lead times but can also reduce costs associated with traditional mold production methods.
The integration of 3D printed components with silicone molds can also yield hybrid solutions that take advantage of both technologies, such as custom-built inserts for complex shapes or improved heat distribution in culinary applications.
Looking towards the future, the intersection of silicone molding and 3D printing will further democratize the craft, offering more individuals a chance to create specialized molds tailored to their unique needs.
In summary, the future of silicone mold technology looks promising, with material innovations and advances in 3D printing promising to reshape industries. Enhanced durability, eco-friendly materials, and rapid prototyping are just the tip of the iceberg, paving the way for new applications and possibilities for silicone molds.
Finale
The conclusion serves as a pivotal component of this comprehensive guide, encapsulating the overarching themes and insights conveyed throughout. In contemplating the significance of silicone molds, it becomes evident that they are more than mere containers for casting; they represent an amalgamation of innovation and practicality.
Recap of Key Insights
Silicone molds offer a solid advantage due to their flexibility and durability, allowing creators to produce intricate designs without the key drawbacks associated with traditional materials. They provide ideal insulation, making them suitable for various temperatures, while their non-stick nature ensures easy demolding. The cost-effectiveness adds another layer of appeal, especially for those venturing into custom projects. Notably, the manufacturing methods have evolved, integrating modern technology like 3D printing, enhancing the capability to produce tailor-made solutions efficiently.
"In the hands of both amateur and seasoned professionals, silicone molds serve as a potent tool for creativity and functionality."
Encouragement for Exploration
For investors, developers, and managers alike, engaging with the world of silicone molds opens a treasure trove of possibilities. As industries continue to explore new applications, from culinary arts to manufacturing, it is crucial to stay abreast of current trends and innovations. Experimenting with different designs and applications can lead to discoveries that may not only enhance production processes but could also lead to new avenues of revenue. Taking the plunge into customizing molds can seem intimidating, yet it also represents an opportunity for differentiation in a market that values originality.
In summary, embracing the use of silicone molds not only enhances creative potential but also aligns with modern manufacturing principles that prioritize efficiency and adaptability. With a clear understanding gained from this guide, you are now equipped to delve deeper into the diverse applications and innovations that silicone molds have to offer.